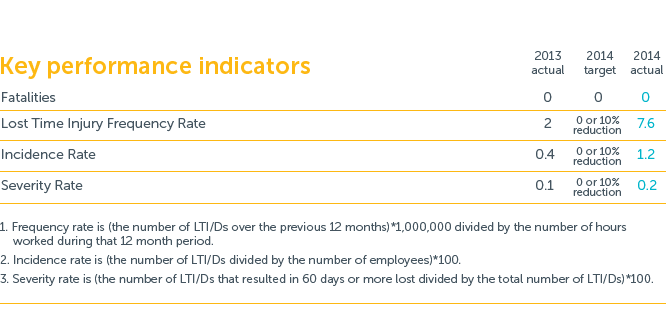
Key Achievements
Safety, Health and Wellbeing Strategy
Our three-year Safety, Health and Wellbeing Strategy is being rolled out across the organisation. It guides us towards a more mature safety culture where complacency is continually challenged, supporting our commitment to providing a safe and healthy work environment for our people.
Management Systems
We have employed a multi-layered committee structure across the organisation to ensure that we are aware of our risks and can manage them effectively. These committees comprise executives, senior management, employees and elected safety and health representatives.
Our management plans are based on corporate initiatives, local issues and consultation and are communicated to the organisation, along with emerging SHW matters and upcoming events, through a communique published on our intranet.
We take the position that safety is everyone’s responsibility and as such encourage a proactive safety culture through participation. All corporate policies and procedures are reviewed and made available to staff for comment. In some circumstances working groups have been established to consult staff from all areas of the organisation. Initiatives and feedback from the working groups are referred directly to the Corporate SHW Committee for consideration.
Event Reporting System
We have a very diverse operational workforce comprised of employees as well as staff from a range of contractors that undertake work on our behalf. Keeping this in mind, the assurance of safety, health and wellbeing for these workers and the preservation of the environment must always be top of mind while we undertake work on infrastructure covering the State.
A new online Event Reporting System will provide transparency around the hazards we face. It will also improve the flow of information across our business and will in turn allow for better decision-making and actions concerning critical SHW aspects.
This system will be used by both Main Roads and our contractors for the primary flow of information including hazards, controls, inspections, investigations, risk assessments, health tests and numerous registers. The system is scheduled for completion in November 2014 with rollout beginning in January 2015.
Performance Insight
We work towards ensuring the safety of our staff by taking a proactive approach to measuring SHW performance.
We’ve looked at the way we measure the safety, health and wellbeing of our business and have made a range of changes to our key performance indicators (KPIs) to better address the challenges of maintaining a safe work environment.
Changes include:
- Integrating additional lead indicators
- Developing appropriate benchmarks to better gauge performance (from an external and internal perspective)
- Providing the business with tools to guide and clarify the integration of KPIs into all levels of the organisation.
The reporting process has been significantly streamlined and more structured data capturing process has also been implemented. These changes have improved the efficiency of the reporting process and allow more reliable and accurate data to be captured and presented to our Executive.
Corporate SHW Management Systems Training
Formally known as ‘OSH for Line Managers’, this is a one day intensive training course customised for Main Roads. The course contains five modules including Safety Law; Safety Management Systems; Hazard Management; Incident and Injury Management; and Safety Leadership, Culture, Communication and Consultation.
The objectives of the course are to make line managers aware of their legal responsibilities and potential exposures to legal risk that could impact on us. The course also aims to provide managers with SHW management skills to enable them to manage SHW systems in their area and effectively carry out their SHW activities. The Corporate SHW Committee insists that all Managers complete this course and undergo refresher training every five years.
Industry Working Group
The Industry Working Group created in 2014 is comprised of our employees and contractors and provides the opportunity to collaborate on current and future SHW industry initiatives and issues. It offers a platform for knowledge sharing between the organisations to achieve greater alignment and continual improvement of each other’s Safety Management Systems.
Business Partnering
We are committed to providing the appropriate support and guidance to our external and internal stakeholders. To facilitate this, a matrix management structure is employed where a resource (business partner) is integrated into the appropriate areas of the organisation.
Business partners implement corporate SHW systems and processes and coach and mentor others to build technical and leadership capability to support strategic SHW business objectives.
Third Party and Work Safe Plan Certification
Our Occupational Safety and Health Management System (OSHMS) was assessed and recommended for re-certification to Australian Standard 4801 in June 2014. Corporately, we proudly maintain our WorkSafe Plan – Gold Certification.
Taking Proactive Safety, Health and Wellbeing Preventative Measures
We take a proactive approach to helping our people manage their health and wellbeing and as such we continue to expand upon our health and wellbeing program inclusions.
Current initiatives that we offer as part of the program include 1 on 1 health and fitness consultation, healthy heart checks, fitness programs and blood pressure screenings.
Our Corporate Health and Wellbeing Calendar gives employees the opportunity to participate in community charity events such as the City to Surf, Freeway Bike Hike, Great Bike Ride, HBF Run for a Reason and various State Government endorsed Corporate Cup activities. The Corporate Calendar also notes dates for National Awareness campaigns such as R U OK Day, Biggest Morning Tea and Stroke Week. We encourage staff to take part in organised activities to raise funds for such charities or to participate in presentations or activities that will assist in raising awareness and promoting healthy behaviours or interventions.
In addition to the resource centre for accessing health and wellbeing information, we continue our commitment to providing a confidential Employee Assistance Program. This is an organisation-funded counselling service which provides support to employees who may be experiencing problems, affecting their job performance or personal lives.
Flu vaccinations, skin cancer screenings and Healthy Heart checks were once again offered to employees, with a total of 728 participating across all three programs. We also aim to educate staff on current health topics through presentations, regular screenings and one-on-one consultations.
Lost Time Injuries
Lost Time Injury/Day (LTI/D) is defined as an injury or disease that results in the affected employee being unable to work for one full shift or longer. The following graphs show our performance and that of our contractors during the year:
The numbers:
- Main Roads – 15 LTI/D sustained, resulting in a Lost Time Injury/Disease Frequency Rate (LTIFR) of 7.6 serious injuries sustained per million hours worked
- Contractors – 25 LTI/D sustained resulting in their LTIFR of 4.5 serious injuries sustained per million hours worked
Although our ultimate goal is for zero harm, we have had an increase in the number of lost time injuries this year.
The majority of serious incidents involved vehicles, equipment, and manual tasks/ergonomics. In the next year, we will again be focusing our attention on minimising the likelihood of these risks recurring. A breakdown of our incidents by type is outlined below.
Summary of all incidents by type and severity
Incident Types | Lost Time Injuries | Non Lost Time Injuries | Near Miss Incidents | Total |
Vehicle | 0 | 1 | 13 | 14 |
Equipment | 1 | 7 | 13 | 21 |
Ergonomics/Manual Tasks | 7 | 9 | 13 | 26 |
Other | 3 | 4 | 5 | 12 |
Slips, Trips and Falls | 3 | 8 | 2 | 13 |
Human Factors | 0 | 1 | 6 | 7 |
Bites/Stings | 0 | 2 | 0 | 2 |
Environment | 0 | 2 | 1 | 3 |
Health | 1 | 0 | 1 | 2 |
System Failure | 0 | 0 | 1 | 1 |
Total | 15 | 34 | 55 | 104 |
---|
Workers’ Compensation and Injury Management
We are committed to maintaining the safety, health and wellbeing of all employees and in achieving this we adopt a proactive and supportive approach to injury management.
The numbers:
- 20 workers compensation claims received
- 9 finalised
- 1 pending
- 1 declined
83% of our injured workers returned to their pre-injury role and volume of hours within 13 weeks and 17% returned between 13 and 26 weeks of sustaining their injury. The graph below illustrates the total number of lodged claims in this financial year compared to previous years.
Looking Ahead
- Review the Safety, Health & Wellbeing Management System in alignment with the impending Workplace Safety and Health Laws (WA).
- Roll out an electronic hazard and incident reporting management systems for employees and contractors.
- Continue to build the maturity of Main Roads’ safety culture around personal responsibility.
- Create a safety cultural program.
Any innovation involves an element of risk, and appropriately managing that risk without stifling new ideas is a common challenge for the public sector. Read More
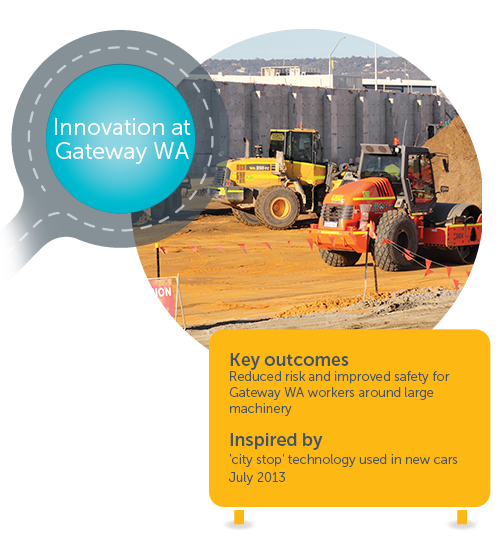
Any construction project carries with it inherent risks for workers. One such risk is working around mobile plants especially when undertaking asphalt activity. Previous attempts to mitigate this risk involved the use of a personal alert device that informed plant operators when a person got too close to a machine. However it was found that the slow processing of information allowed people to get dangerously close to a machine before an alert sounded. So a better way was needed to manage the risk.
After research, testing and consultation, it was decided that full machine intervention, triggered by proximity sensors to identify when an object or person was too close to a machine, was the most effective solution. Similar technology has been used in new cars through the ‘city stop’ feature where potential collisions are avoided through automatic braking triggered by sensors in the vehicle.
This technology had not been used with large machines by anyone in the construction industry. It was generated, developed and trialled in collaboration with the Gateway WA team to reduce risks and improve safety in this critical area. Following its completion in 2014, the trial will be assessed to determine if we will implement this approach on other sites.
The trial is a prime example of how the process for selecting and implementing innovation projects connects with our new Safety, Health and Wellbeing Change Management procedure to streamline and promote innovative ways of improving safety across all our projects.